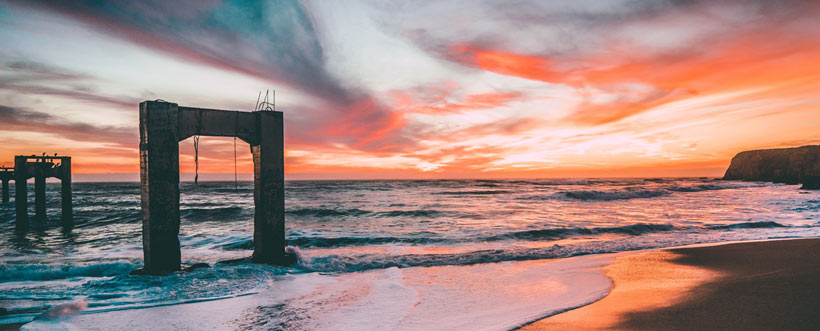
OHSAS 18001: acciones correctivas en un SG-SST
En el artículo de hoy vamos a centrarnos en la norma OHSAS 18001 que regula los principios en lo que se han de basar los Sistemas de Gestión de la Salud y Seguridad en el Trabajo y las acciones correctivas en un SG-SST que pueden tener que poner en marcha las organizaciones.
Las acciones correctivas y preventivas ayudarán a que los Sistemas de Gestión de la Seguridad y Salud en el Trabajo sean eficientes. Algunos ejemplos de tales acciones los recogimos en el artículo “Algunos ejemplos de acciones correctivas en Gestión de Calidad”.
Muchas personas consideran que las acciones correctivas y preventivas suponen pérdida de tiempo para las organizaciones. Sin embargo lo que no saben o no entienden es que es gracias a las mismas que se puede asegurar que los Sistemas de Gestión de la Salud y Seguridad en el Trabajo estén funcionando siempre de manera óptima.
A la hora de aplicar las acciones correctivas y preventivas, algunas empresas cuentan con sistemas eficaces. Cada empresa puede tener su propio sistema. Nosotros hoy vamos a pasar a detallar y analizar el llamado Sistema de Acciones Correctivas y Preventivas de siete pasos para mejorar su sistema de gestión de Seguridad y Salud en el Trabajo.
[widget id=»text-71″]
Cómo utilizar el proceso de acción correctiva de 7 pasos en OHSAS 18001
Vamos a ver cómo podríamos aplicar este sistema de 7 pasos de acciones correctivas, a un ejemplo concreto, suponiendo que hemos descubierto un problema en el Sistema de Gestión de la SST de nuestra organización.
Contar con procesos de acciones correctivas en lugar de meras correcciones cada vez que se detecte un problema repetitivo, puede ayudar a encontrar la mejor recuperación de la inversión (ROI).
Utilizando el proceso de 7 pasos con OHSAS 18001
Veamos a continuación los pasos a seguir para aplicar el procesos de 7 pasos de acciones correctivas y preventivas en OHSAS 18001:
Paso 1 Definir el problema: para ello, lo adecuado es usar expresiones del tipo “debería ser” y “tal como se encuentra” para definir el problema que has encontrado. Si no eres capaz de identificar cómo deberían ser las cosas, es posible que no estés identificando un problema. Para ir viéndolo mejor, pongamos como ejemplo el siguiente:
- Debería ser: los equipos de protección individual (EPI) se deben usar para dispensar los productos químicos en la campana de humos.
- Tal como se encuentra la situación: en la auditoría realizada, se detectó que 2 de 4 operadores no usaron los EPI durante la operación.
Paso 2 Definir el alcance del problema: en el ejemplo que estamos siguiendo, vamos a suponer que en investigaciones de procesos similares no se detectaron casos en lo que los EPIs no se estuvieran usando según las instrucciones. Por tanto, diríamos que el alcance del problema detectado y que ya hemos definido (según el paso 1) tiene como alcance sólo esta operación concreta de distribución de productos químicos.
Paso 3 Contener el problema: en este paso es dónde se le da solución instantánea al problema detectado. En nuestro ejemplo, la solución podría ser volver a formar a los operadores del proceso concreto en el que se ha detectado el problema, o bien colocar señalizaciones para recordarles las instrucciones de uso.
Esto son como hemos dicho soluciones inmediatas, es decir, de corto plazo. Sin embargo, habrá que asegurarse que el problema también se resuelve a largo plazo.
Paso 4 Buscar la causa raíz del problema: si no se llega a la raíz que origina el problema, todas las soluciones que se pongan en el paso anterior serán en la mayoría de las veces de corta duración. Este paso encierra mayor dificultad que los demás. Existen muchos métodos para encontrar la raíz del problema. Nosotros, concretamente, en este post vamos a hacer mención al llamado método del diagrama de espina de pescado. Este básicamente consiste en definir todas las posibles causas del problema en cuestión, para ser revisados e ir eliminando hasta quedarnos con la causa definitiva que generó el problema.
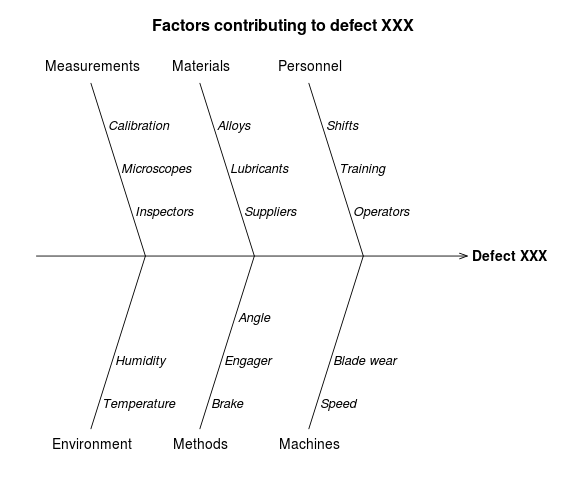
Paso 5 Planificar la acción correctiva: en el ejemplo que estamos analizando, se ha decidido en el plan de acción que se instalen unos tableros informando de los EPIs que han de utilizarse y que sean perfectamente visibles en el puesto concreto. De esta forma se reduce la probabilidad de que vuelva a suceder el problema.
Paso 6 Poner en práctica su plan: en este caso en concreto, la puesta en práctica, consistiría en obtener las tablas, ponerlas en el lugar adecuado, mantenerlas visibles y actualizarlas cuando se vea que se van desgastando.
Paso 7 Asegurarnos de que el plan funciona con acciones de seguimiento: este paso es esencial, ya que una vez implementado el plan es necesario revisar el proceso para ver que ha funcionado. Es este úlitmo paso, son muchas las empresas que fallan.
En nuestro ejemplo, sería que en las siguientes auditorías se verifique que los EPIs se están usando como dictan las instrucciones.
En caso de que el problema continúe, sería necesario volver a analizar el origen del problema.
Software OHSAS 18001
Para asegurarnos que nuestro Sistema de Gestión de Seguridad y Salud en el Trabajo es eficaz a la vez que eficiente una buena forma es decidir automatizar el mismo mediante herramientas como el ISOTools Excellence. Este software da respuesta a los requisitos que contiene la norma OHSAS 18001, logrando de esta forma cumplir de forma excelente con el objetivo de reducir y prevenir los accidentes laborales.
[widget id=»text-70″]
¿Desea saber más?
Entradas relacionadas
Circular 3335 Al finalizar el año 2017 se publicó la circular 3335. La normativa de seguridad laboral entró…
Algunas cosas se pueden comprar sin hacer mayores preguntas. Un software para gestionar el Sistema de Cumplimiento no…
Hemos hablado de la importancia del plan de respuesta a emergencias, de las características que este documento debe…
La automatización del control de documentos es una necesidad apremiante para muchas organizaciones que, a diario, reciben y…